Reports and articles
Digital manufacturing: opportunities and barriers
Published on November 19th 2019
The opportunities presented by technological transformation are significant, but the obstacles are challenging, and the threat of disruption from new types of competitors with innovative business models is high. How can manufacturers respond to the changing landscape, and how can policymakers best support organisations towards growth and productivity? Dr Carlos López-Gómez and Dr David Leal-Ayala of the IfM’s Policy Links Unit provide an overview of the unfolding digital revolution, and share insights from their work with governments and multinational organisations…
Responding to the changing face of global industry
The opportunities from digital manufacturing are real – but so are the challenges
Emerging technologies are radically reshaping manufacturing. Companies are changing how they make products, the business models they adopt, how they interact with suppliers and customers, and even how they innovate. There is new potential for enhancing productivity, for stimulating innovation, and for generating products and services which create new demand and markets.
In manufacturing, digital transformation goes far beyond automation on the factory floor, also enabling faster research and development, closer integration across supply chains, and increased customisation of products and services. New technologies offer the potential to use resources more efficiently, improve the safety of production processes, and address supply constraints. The extent of the potential changes heralded by these opportunities (and competitive threats) points to the likely need for a paradigm shift in companies’ manufacturing strategies.
At governmental level, the digital revolution in manufacturing poses opportunities and challenges in key policy areas such as employment, productivity, competitiveness, and sustainability.
Individual digital technologies are each likely to have a significant impact on their own, but it is their convergence and integration that makes them so disruptive. Although there is no consensus on its potential impact, estimates from the World Economic Forum suggest digitalisation could create US$100 trillion of value to industry and society over the next decade, and according to the European Commission, European industry could gain €110 billion per year from digitalisation.
The digital revolution is expected to change what skills are required from the future workforce, causing significant disruptions in the labour market. High numbers of jobs are likely to be lost, displaced, or created, and while it is difficult to put numbers against these, high estimates reflect a common perception about the large-scale impact of digitalisation worldwide[1,2]. There is significant variation between international studies in predicted impact on jobs due to automation: figures go from the creation of over 100 million jobs to the loss of over 200 million.
Digitalisation also brings important concerns about the cyber security of industrial systems. It also threatens to disrupt business models in important sectors of the economy, and raises increased threat from new breeds of competitors gaining market share. Data and privacy are increasing concerns for firms and for consumers, with difficult questions around the ownership of the immeasurable volumes of data being generated. Fundamentally, the digital transformation of manufacturing increasingly necessitates companies, industries and countries to reassess whether their manufacturing systems are ready to compete effectively given the potentially disruptive changes brought about by digitalisation, in the context of increasingly interconnected global value networks[3].
What is the ‘digitalisation of manufacturing’?
By Dr Eoin O’Sullivan, Director of the IfM’s Centre for Science, Technology & Innovation Policy (CSTI)
The ‘digitalisation of manufacturing’ is also commonly termed the ‘fourth industrial revolution’ (or 4IR). It refers to the use of digital technologies, data and applications to deliver advancements in manufacturing-related operations (including the broader value chain of manufacturing activities), to enhance the performance of manufactured products (and related services) in both established and emerging sectors. The family of technologies underpinning digitalisation includes: cloud computing; advanced sensors; high-performance computing; advanced automated and autonomous systems; robotics; artificial intelligence; machine learning; augmented/virtual reality; blockchain; big data; and digital fabrication (including 3D printing), among others.
The potential for improved productivity and competitiveness is emerging through the convergence of these technologies into applications and solutions, through:
- Improved sensing/interacting with the physical world
- Enhanced organisation/sharing/analysis of data
- Better connectivity/networking/control (of industrial-innovation activities)
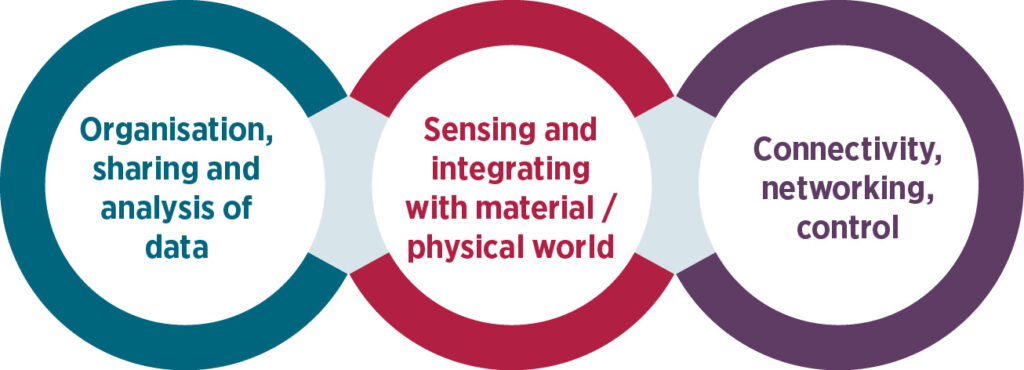
The term ‘Industry 4.0’ has gained widespread international currency, including by governments, global companies, and the media. The term originates from the strategic initiative of the German government’s High-Tech Strategy (‘Industrie 4.0’). This anticipates the impact of a fourth industrial revolution whereby cyber-physical systems, the Internet of Things, and big data will more effectively connect and integrate manufacturing systems.
Opportunities for value capture from digital manufacturing
We have identified four manufacturing ‘dimensions’ of opportunities, corresponding to different types of innovation:
- Product / service innovation – offering new and more functional products and services, and new business models that create value from digital data and capabilities.
- Process innovation – achieving higher levels of factory efficiency and more flexible production processes driven by vertical digital integration.
- Supply chain innovation – more integrated and optimised supply chain capabilities driven by horizontal digital integration.
- Product / service design and delivery – superior understanding of demand, more customer-led design and delivery using digital platforms, and higher levels of customer satisfaction.
The multiplicity of opportunities for value capture is taking different forms in distinct industrial sectors and types of firms. Figure 1 illustrates examples of such opportunities across the four manufacturing dimensions identified.
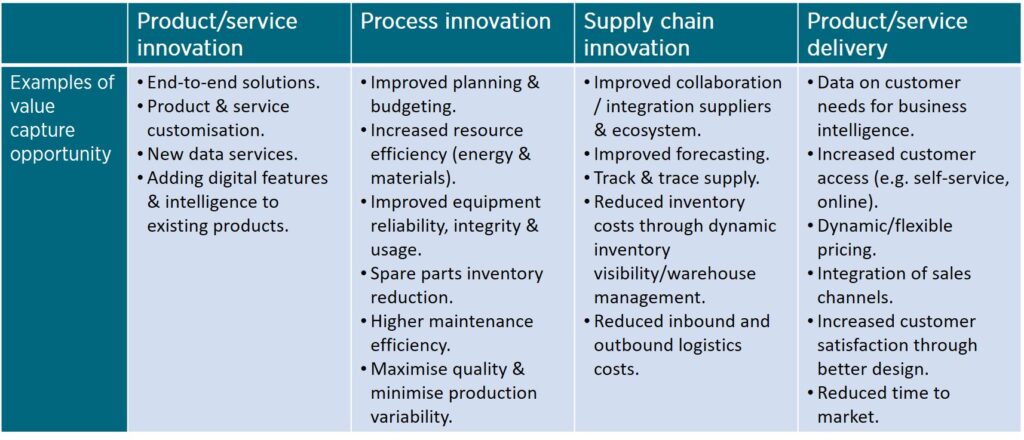
Barriers to value capture for firms
However, successful deployment of digital technologies is not an easy task. In our research we have identified several types of barriers to technology deployment:
- Individual people barriers: Including the gaps in the skills and competencies of workers, lack of knowledge and awareness of decision-makers, insufficient problem-solving capabilities, aversion to risk and/or change.
- Organisational barriers: Including the lack of a clear plan or roadmap for identifying technologies which help to deliver business objectives, and for implementation. Organisational culture, risk aversion, lack of innovation capability, or short-term focus can be significant obstacles.
- Technical barriers: Such as the lack of availability of appropriate existing solutions, and lack of technical competency for implementing new applications, as well as difficulty integrating new technologies with existing systems.
- Market barriers: Including the difficulty of creating awareness and demonstrating functionality of new solutions among industrial users, or resistance among supply chain partners; or market readiness of new technologies.
- Economic/financial barriers: Such as uncertain or weak wider economic conditions, and limited organisational resources or willingness to invest.
- Regulatory/policy barriers: Including the lack of innovation policies to support firms, heavy regulation in some sectors, or costly audits/certification requirements which make it harder to reconfigure existing systems.
The challenges described here are just a small sample of the many difficulties that could prevent manufacturing sectors and firms from capturing value from new industrial digitalisation trends. Another helpful way of classifying the range of challenges and barriers to value capture is by framing the discussion in terms of the three fundamental stages of innovation: knowledge generation, diffusion and deployment, as shown in Figure 2.
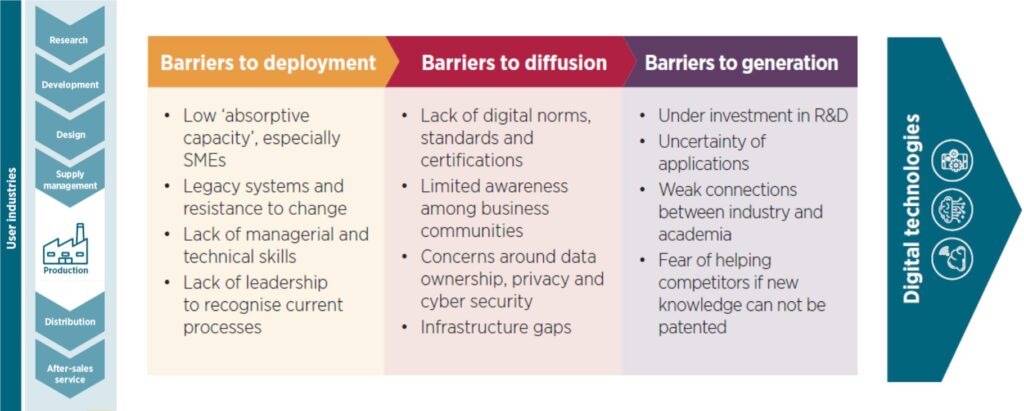
Source: Policy Links Unit/Centre for Science, Technology & Innovation Policy, IfM
Strategies for mitigating the barriers
So how can policymakers and firms identify and mitigate barriers, and open up the opportunities presented by digitalisation in manufacturing?
Our research shows that the set of barriers can vary substantially between different regions, sectors, firms, and technology applications. There are no one-size-fits-all solutions. We are working to develop and refine a framework intended to help the development of policy initiatives to support innovation and technological development. The framework can be used to evaluate which barriers are present in a given technology deployment setting, and to identify how to mitigate these barriers.
For example, mitigating strategies initiated by policymakers to address ‘organisational barriers’ (as described above), might include:
- Increasing strategic awareness about digitalisation trends.
- Providing frameworks for changing business models.
- Supporting organisational orientation towards the problem, not the solution.
- Supporting the elaboration and dynamic improvement of roadmaps.
- Diagnostics related to a specific firm’s contingencies.
- Using demonstrative cases for supporting cultural change.
- Giving support for improving innovation capabilities.
- Supporting system integration.
Digital manufacturing technologies can have a cross-cutting and disruptive effect across manufacturing sectors. By understanding the opportunities, identifying the barriers to adoption and planning mitigation strategies, both policymakers and organisations can move towards exploiting the huge potential value of digital transformation.
1 -World Economic Forum (2016). Digital Transformation of Industries: Societal Impacts.
2 – The UK Made Smarter review, for example, estimates a potential net gain of 175,000 jobs throughout the UK economy over the next decade.
3- Global value networks can be defined as complex systems of interconnected (and geographically dispersed) firms that deliver value to end users, operating across the full range of business activities. Source: Adapted from Srai, J. and Christodoulou, P. (2014). Capturing Value from Global Networks. Institute for Manufacturing (IfM).
4 – López-Gómez, C.E, Leal-Ayala, D.R., Palladino, M. and O’Sullivan, E. (2017). Emerging trends in global advanced manufacturing: challenges, opportunities and policy responses. United Nations Industrial Development Organisation / Policy Links / IfM.
For further information please contact:
Carlos López-Gómez
+44 (0) 1223 764657cel44@cam.ac.ukConnect on LinkedInRelated resources
17th June 2025
Shaping inclusive digital and green transitions in working life
10th June 2025
Digital trade in Southeast Asia: How perceptions of data risks shape policymaking
News | 5th June 2025